早稻田大学理工学术院的竹泽晃弘副教授等人组成的研究团队宣布,开发出了减少金属3D打印热变形的方法。通过在内部优化设计晶格构造(中空构造),成功地减少了成型物体的变形。该方法有望减少大型结构物成型过程中变大的变形。相关成果已经发布在国际科学期刊《Additive Manufacturing》11月6日号上。
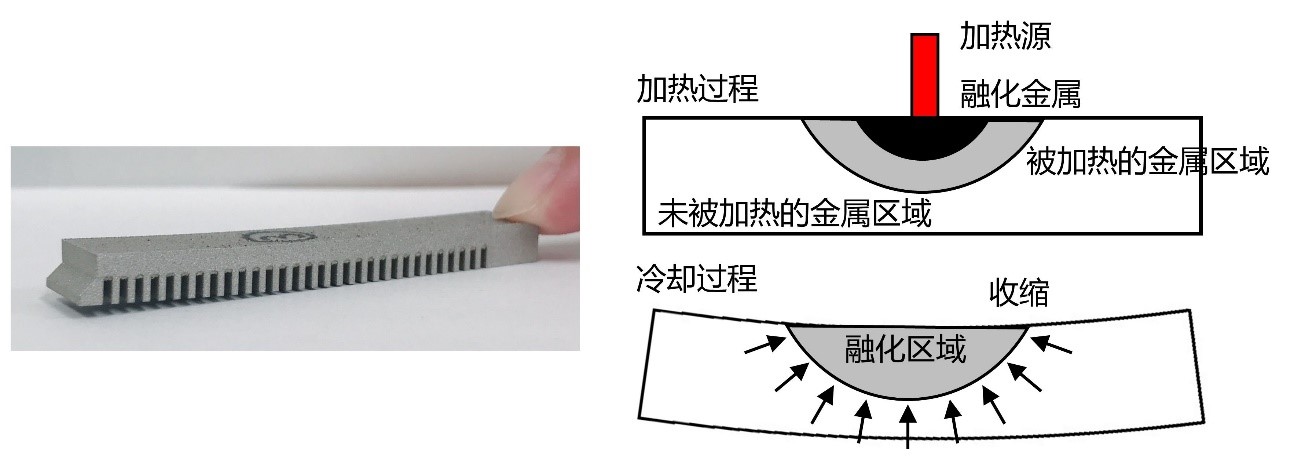
最佳晶格结构造型物(a)与截面图(b)(供图:早稻田大学)
近年来,金属3D打印作为新一代加工技术得到了应用。普及最为广泛的金属3D打印是通过反复用激光熔化和凝结金属粉末薄层来形成三维结构。但在这个过程存在熔化凝结处冷却后会产生较大的收缩应变的课题。当将造型物与底座分离时,应变会引发严重的翘曲,从而导致产品不合格。对此,人们一直通过在造型时预加热来减小熔化与冷却时的温差,以及优化激光的扫描路径等来减轻热变形。
此次,研究团队为了进一步减轻少变形,开发了在金属3D打印的造型对象内部设计名为晶格的中空构造的方法。实际制作模型后确认,通过优化配置晶格可以减少变形。一般来说,只要在模型内部设置中空构造就可以分散张力,减轻热变形,而研究团队分别制作了晶格均匀分布的模型和利用新方法优化晶格分布的模型进行了比较,发现晶格优化分布的模型翘曲量减少了10%以上。
开发该方法时,还利用造船领域使用的近似计算焊接变形的简单递归关系式,来表示固有应变的方法。另外,通过利用结构优化法之一的拓扑优化算法,还成功开发出了旨在减轻热变形的晶格分布的优化方法。
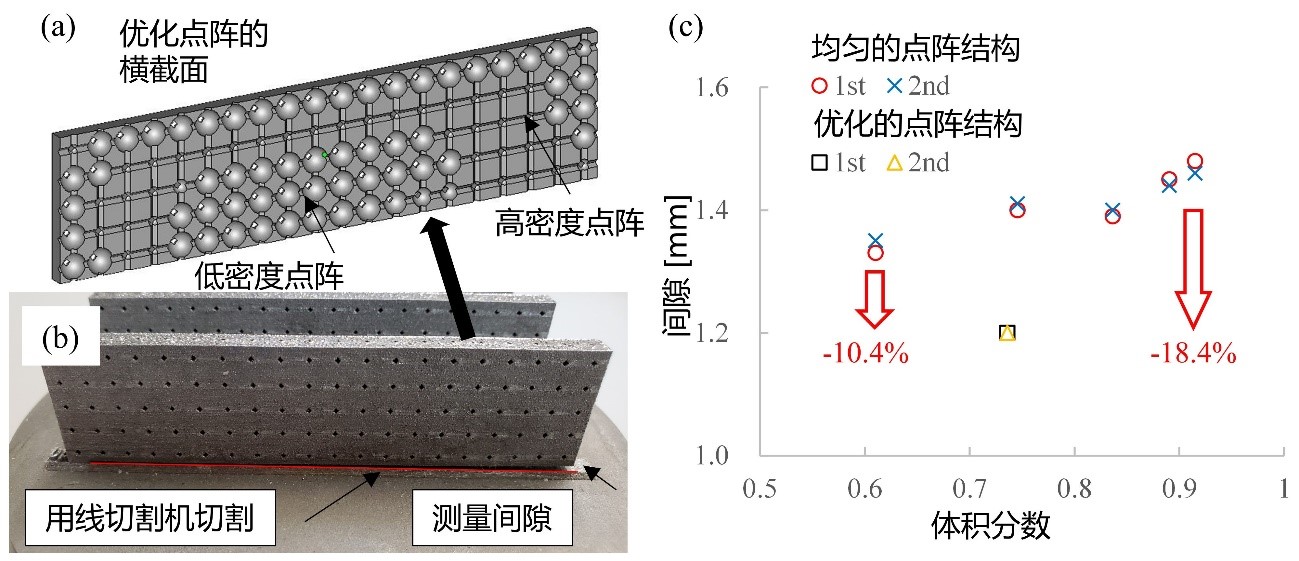
利用拓扑优化算法优化晶格分布(供图:早稻田大学)
新开发的方法可以在模型内部形成空心球状的晶格结构。此次虽然形成了球状晶格结构,但形状会因3D金属打印机的兼容性而异。模型由晶格大量分布的低密度点阵区域和没有晶格结构的高密度点阵区域构成。模型内部还形成了与晶格相连的格子状中空结构,这是用来在形成中空结构时去除金属粉末的。
该方法与现有的减少热变形方法相结合的话,还可以实现更优异减少的热变形的效果。
竹泽副教授表示:“目前正研究优化现有的激光扫描路径。结合使用此次开发的技术,相信可以进一步改善热变形问题。”
原文:《科学新闻》
翻译编辑:JST客观日本编辑部